Quick video of Daniel's leak test: https://spectra.video/w/bSYUyYpJVr34N92261cd6K
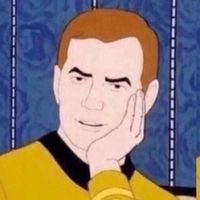
kirk
Posts
-
Designing the large-format cell -
Designing the large-format cellThe current collectors and endplates as-received from SendCutSend in the US, laser-cut and milled, respectively:
Some more pics:
-
My build (very slowly progressing)@czahl ah I think @danielfp248 would know this answer, he has flashed most of the firmware but I don't remember him saying he made any changes. He is traveling right now so it may take him a bit to get back to us. I have only used the MYSTAT, I haven't dealt with the firmware myself. If he made any changes then we can push them to the repo ASAP.
-
Blog: czahl's buildThis is possible, but we haven't tried. We've been able to seal it with silicone gaskets so there's been no need. Also, if one of the gaskets gets damaged, it's simple to replace, unlike resealing the flow frame. But there's no reason you can't try!
"Ironing" the top layer of the print in your slicer may also make it smoother, or manually sanding, but again we haven't found it necessary to try this
-
My build (very slowly progressing)Also actually @danielfp248 made all the code improvements to the repository for MYSTAT, he just dislikes Git and so I'm the one who uploads them
-
My build (very slowly progressing)I am less familiar with the MYSTAT hardware/firmware, that repository is a fork and you can see the original developers efforts much before mine! Just to say I'm not super familiar, @danielfp248 programed mine and sent it to me in the mail
Yes, the main PSU needs to be connected for current measurents to function.
Also a warning, make sure the MYSTAT is completely powered off and unplugged before inserting/removing the measurement cable to the MYSTAT, otherwise there is a risk of damage.
Are you following the calibration procedure from the original paper with a (IIRC) 1k resistor?
-
Blog: czahl's buildYeah, nice work @czahl ! And another +1 for a drag knife being more appropriate than milling, but, it's worth giving it a go anyway! Laser cutter also possible, for gaskets, but no guarantee on the safety of fumes. IIRC cutting grafoil with a laser is possible only with a fiber laser, not CO2.
-
MyStat PCBs for free@sepi @czahl @danielfp248 I have enabled the chat plugin just now! With min. user reputation of 2 to try to prevent spam.
Public and private chat groups/PMs now possible, though I don't think it's encrypted if that's a concern (we are hosted by NodeBB).
-
Designing the large-format cell@muntasirms oh this looks great, I hadn't seen the paper! It's exactly what we need for the non-shunt-current related issues (which are another bridge for us anyway, down the road). An efficient manifold seems like it could be decoupled from the shunt current protection scheme also. I will try to implement it in FreeCAD.
-
Designing the large-format cellSome preliminary CFD of the simplified flow frame (U in m/s and P in Pa if I understand OpenFOAM correctly)
Conditions
- 4 L/min volumetric flowrate through one half-cell, inlet is on the top left, outlet on the lower right.
- Ambient pressure on cell outlet
- No-slip wall
- File containing CAD and CFD simulation setup is here
Blue is inlet, red outlet, pink is porous zone
!
Close-up of mesh:
Flow Distribution (m/s)
Pletcher and Walsh say a range of 0.05-0.4 m/s linear velocity is a good design range for electrolyte flow, if I apply a smaller range for velocity with 0.05 m/s as the upper limit, we see which areas in red have sufficient flow and where the dead zones are (in the corners, predictably)
Pressure Drop (Pa)
Big Caveat
Still need to calculate the Darcy-Forchheimer coefficients to do the porous zone simulation in the graphite felt, right now I am using the default values, which are almost certainly not correct. If anyone feels like finding that data (https://openfoamwiki.net/index.php/DarcyForchheimer). I think Antoni Forner-Cuenca's group has measured a lot on this recently. This could change the results quite a bit as far as flow distribution and pressure drop. I've mostly so far just been getting familiar with the simulation pipeline in FreeCAD --> CfdOF --> OpenFOAM --> ParaView.
Design is far from final, and I'm probably doing the CFD incorrectly, BUT it prints and doesn't leak! We will keep optimizing the flow frame later.
-
Blog: czahl's build@czahl said in Blog: czahl's build:
the new update from @kirk where the inner diameter is increased from 2 to 3mm.
Also good catch, @danielfp248 has tested this already and it results in smoother flow/less pressure drop in the system without introducing new leakage it appears.
-
Blog: czahl's buildNice progress, sorry that PP printing is such a pain, but if it's any consolation, this is the norm when finding a setup that works. We really hope to find a DIY-friendly chemistry soon that could work with ABS or other easier-to-print plastics!
-
Adopting the Contributor CovenantHi all,
It's been very exciting to see the FBRC community grow these past months! We have come a long way from just two people tinkering in their respective apartments. If we are going to develop a practical battery technology in this way, having a strong open-source community will be crucial.
So far, all the interactions here have been positive to my knowledge. We've only had one blatant spam post so far. A few people I spoke with recommended adopting a code of conduct, such as the well-used Contributor Covenant. I have uploaded it to the FBRC website here and added the contact info for the current mod team (right now, me and @danielfp248).
I'm not adding this in response to any recent incident, rather, I think it's good to have it established and in-place as the community continues to grow.
If you have any comments or feedback on this, please feel free to discuss here! It's not a static document; we can change it as we see fit.
TL;DR: Don't be a jerk, let the mods know if someone is causing trouble, and let's make open-source batteries happen!
-
My build (very slowly progressing)@sepi said in My build (very slowly progressing):
I'm more and more considering printing my own centrifugal pump with magnetic coupling. This could also be interesting for the larger models as good pumps seem to be pretty expensive.
If you do, please share the results! This may be very demanding of PP FDM printing (leaktightness, tolerances, etc.). For reference, these are the pumps we are planning on using for the large-format cell (they are likely too large, but the smallest PP, mag drive centrifugal pumps we could find): https://fbrc.nodebb.com/post/30. They were less than 50 EUR each at a quantity of 2 pumps, IIRC.
-
My build (very slowly progressing)@danielfp248 said in My build (very slowly progressing):
@kirk Thanks for clarifying kirk, I have the same issue, lol.
I have added a note to the docs on this now!
Also @sepi I somehow missed reading the main chunk of your thread that you posted several days ago - great work!!
@sepi said in My build (very slowly progressing):
Now I need to be patient about the Pumps from Kamoer which have't shipped yet
@quinnale has also tried some 3D-printed peristaltic pumps in his build thread: https://fbrc.nodebb.com/topic/23/towards-a-working-system
@sepi said in My build (very slowly progressing):
So I finally printed my modified jig in 6h on my kobra max with 1mm nozzle. This made it quick but fugly. You judge for yourself and maybe tell me why my modifications don't make sense.
Can you show the back of your jig? If the rear support doesn't stick out long enough, the entire jig can tip over once the pumps are installed due to a shift in the center of gravity.
Also, it looks cool and wavy! And using a lot less material. Did you modify it in FreeCAD?
-
My build (very slowly progressing)@sepi said in My build (very slowly progressing):
The button does not work, it's just a tiny bit short. Maybe because my UNO is super old and used a different button.
FYI, that button is upside down which is why it doesn't work! You assemble it so that the large end is fixed inside the case (a bit of a balancing act during the assembly). The original designer has some photos of it assembled here: https://www.thingiverse.com/thing:628929
-
Alternative Electrolytesthanks for this info! FYI I forked your post into a separate topic into the "Electrolyte Development" category just to keep the intro thread relevant.
I am a big fan of Savinell's and Wainright's work at Case! Savinell was on on the all-iron RFB development quite a long time ago... this is one of my highlights from one of his papers in 1981 (!):
Source:
Hruska, L.W. and Savinell, R.F. (1981). Investigation of Factors Affecting Performance of the IronβRedox Battery. Journal of The Electrochemical Society. https://doi.org/10.1149/1.2127366.Showing quite clearly the issue of iron kinetics, even at 60 C...
@muntasirms said in Alternative Electrolytes:
In flow batteries, any time you have plating you end up re-tying power density and energy density through that half cell.
Yes, unfortunately, would love to have an all-liquid configuration that plays well with porous separators but asides from iron-chromium (which also has its own set of cons, like HER/high purity req's) there isn't much out there that's easy to start with, which is why we're starting with zinc to get things going.
@muntasirms said in Alternative Electrolytes:
They attempted to scale but really struggled with having a performant enough slurry electrode that wasn't too viscous.
I saw this, I think I skimmed their ARPA-E report (https://www.osti.gov/biblio/1506426) and they also had issues with the cell plugging. IIRC they also licensed the tech to an Australian company?
@muntasirms said in Alternative Electrolytes:
Have you guys looked into water-in-salt electrolytes? They involve dissolving a ton of a supporting electrolyte to the point where they lower the activity of water and suppress HER. I've seen some work using acetate salts and this one using magnesium chloride to support even iron plating - and I've replicated it successfully. The study plates on copper like I mentioned earlier, but I also got it to plate on grafoil.
I am a big fan of this type of electrolyte engineering! The viscosity can also become an issue with this sort of approach too, no? (You are from now the FBRC viscosity expert
) I see in that paper though they only cycle up to 0.5 M [Fe], which is quite low in terms of energy density (~8 Wh/L if I'm not mistaken). But it seems solid enough to at least test in the development kit as an exercise. Also a huge confidence boost that you were able to reproduce it and make it plate on grafoil!
@muntasirms said in Alternative Electrolytes:
I did a little study collecting the centralization/governance of various metals and ranked aqueous battery chemistries by cost and "criticality".
Definitely of interest, would love to see it if you're able to share - it's one of my concerns with iodine chemistries at scale (avoiding artisanal iodine production from seaweed).
-
Systems engineering and modeling@sepi said in Systems engineering and modeling:
Garh, unfortunately I can't read either the Neyhouse paper nor the one I posted sonce I don't have a subscription. Sci-hub and annas-archive also fail me here.
I am an ECS member (who runs the journal it's in) and even I can't get the article
I'll ask around, I'm sure we can find a copy
-
Blog: czahl's buildLooks good! And yes good luck with polypropylene. Like sepi said, the current collector/graphite foil is doing the sealing, not the actual endplate surface, which shouldn't ever contact the electrolyte. I don't think the texture will play a large role.
-
Systems engineering and modeling@muntasirms @sepi PNNL have done a model which includes a Zn-I example system: https://github.com/pnnl/EZBattery/tree/master
Eric Fell also has a 0D model: https://github.com/ericfell/rfbzero, https://joss.theoj.org/papers/10.21105/joss.06537.pdf
I think these could both be good starting points, the former especially for considering the issues @sepi raised in the first post, the latter for understanding more the fundamentals of these systems.