Some great insight here into real-world consumer-scale RFB use from @tserong@mastodon.social ! Great blog btw.
Here are some quotes that stood out to me from this post and some of his previous ones (licensed CC BY-SA)
The (im)practicalities of a hybrid RFB
One of the elephants in the room of academic RFB work is that there are maintenance procedures for plating chemistries which is rarely discussed at benchtop level. Tim goes in-depth into what this means at the practical level.
Redflow batteries are excellent because you can 100% cycle them every day, and they aren’t a giant lump of lithium strapped to your house that’s impossible to put out if it bursts into flames. The catch is that they need to undergo periodic maintenance where they are completely discharged for a few hours at least every three days. If you have more than one, that’s fine because the maintenance cycles interleave (it’s all automatic). If you only have one, you can’t survive grid outages if you’re in a maintenance period
From https://ourobengr.com/2022/07/keeping-the-battery-full/
There are three goals somewhat in tension with each other here:
- Keep the battery full, except during maintenance cycles.
- Don’t let the battery get too full immediately before a maintenance cycle, lest the discharge take too long and maintenance still be active the following morning.
- Don’t schedule charges during peak electricity times (we still want to draw the battery down then, to avoid using the expensive gold plated electrons the power company sends down the wire between 07:00-10:00 and 16:00-21:00).
Here’s the solution I came up with:
- On non-maintenance cycle days, set two no-limit scheduled charges, one from 10:00 for 6 hours, the other from 21:00 for 10 hours. That means the battery will be charged from the grid and/or the sun continuously, except for peak electricity times, when it will be drawn down. Our loads aren’t high enough to completely deplete the battery during peak times, so there will always be some juice in case of a grid outage on non-maintenance cycle days.
- On maintenance cycle days, set a 50% limit scheduled charge from 13:00 for 3 hours, so the battery won’t be too full before that evening’s maintenance cycle, which kicks in at sunset. The day after a maintenance cycle, set a no limit scheduled charge from 03:00 for 4 hours. At our site, maintenance has almost always finished before 03:00, so there’s no conflict here, and we still have time to get some charge into the battery to handle the next morning’s peak.
He then shows us his Python code for implementing this with his power electronics hardware. And it sounds like it works!
CC BY-SA Tim Serong, from https://ourobengr.com/2022/04/go-with-the-flow/
Simon, who knows and understands how the ZCell behaves during maintenance, explained about the Energy Extraction Device, which is part of the unit whose purpose is to deliberately drain the battery down to zero for maintenance in a timely fashion.
It looked like it was the EED being over-drawn, regardless of how much energy was still in the battery. It turns out there’s a thing that the ZCell does to handle surge demand when the EED is on, called an “EED switchback”. ZCells internally have three contactors, for Charge, Discharge and EED (also known as Strip). In normal operation, the C and D contactors are on, and E is off, so the battery can be charged or discharged at will, and the EED is doing nothing. During maintenance, the EED comes on, but it can’t deliver more than 20 amps. If the site pulls more than the EED can supply, the battery goes back to normal operation (C and D on, E off) while the high demand is present. Once the high demand goes away, it switches the EED back on, to keep discharging at the normal rate of 1kW. But, by default, that switchback process only happens five times per battery maintenance cycle so as to avoid the potential for excessive cycling of the contactors in weird edge cases.
The delay did however allow me to spend some time messing around with scheduled charges to see if there was a cost benefit to grid-charging the battery during off-peak times, then drawing it back down during peak, because the reality is we’re going to want to do this in winter when there’s not much sun, so why not try it out in advance? TL;DR: Yes, it’s worth grid charging the battery off-peak, provided you use all that power during peak times, but it’s a bit irritating trying to figure out exactly what you’ll save. In one of my tests it was the difference between paying $3.85 for about 20kWh of usable electricity in a 24 hour period versus paying $4.70, so it’s not insignificant.
That’s about the end of the story. The system is brilliant, and we could not be happier with the support we’ve received from Simon at Redflow, who’s been extremely generous with his time and knowledge, and Murray and Rhys of Lifestyle Electrical Services. Thanks for everything guys, I’ve learned a lot. In the eight months the system has been running we’ve generated 4631kWh of electricity and “only” sent 588kWh to the grid, which means we’ve used 87% of what we generated locally – much better than the pre-battery figure of 45%. I suspect we’ve reduced the amount of power we pull from the grid by about 30% too, but I’ll have to wait until we have a full year’s worth of data to be sure. We’ve also survived or shortened at least five grid outages with durations from a few minutes to a few hours.
The next thing to do is get a second ZCell, and possibly eventually think about a third. Given our current generation capability, two ZCells would allow us to store and utilise 100% of our generated power locally. We’d also have the ability to handle grid outages at any time, because with two batteries the maintenance cycles interleave and they can be configured to always ensure there’s a minimum amount of charge somewhere.
From the linked post above:
Murray needed to come out anyway to replace the carbon sock in the ZCell (a small item of annual maintenance) ...
This leads to the next little bit of fun. The carbon sock is a thing that sits inside the zinc electrolyte tank and helps to keep the electrolyte pH in the correct operating range. Unfortunately I didn’t manage to get a photo of one, but they look a bit like door snakes. Replacing the carbon sock means opening the case, popping one side of the Gas Handling Unit (GHU) off the tank, pulling out the old sock and putting in a new one. Here’s a picture of the ZCell with the back of the case off, indicating where the carbon sock goes:
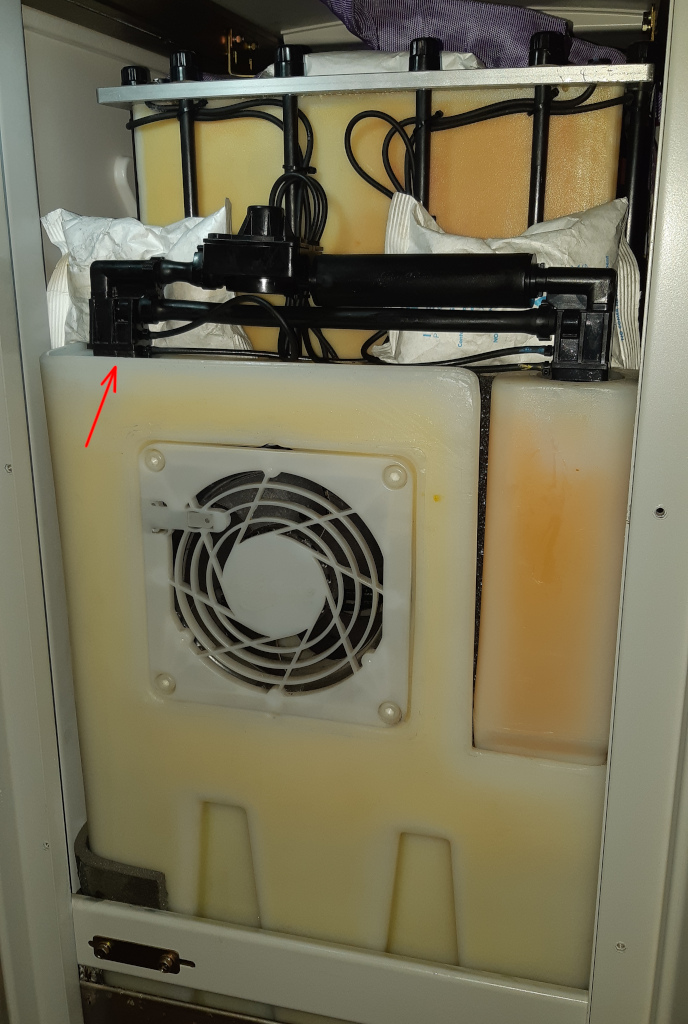
CC BY-SA Tim Serong
"The tank on the left (with the cooling fan) is for zinc electrolyte. The tank on the right is for bromine electrolyte. The blocky assembly of pipes going into both tanks is the GHU. The rectangular box behind that contains the electrode stacks."
When Murray popped the GHU off, he noticed that one of the larger pipes on one side had perished slightly. Thankfully he happened to have a spare GHU with him so was able to replace the assembly immediately. All was well until later that afternoon, when the battery indicated hardware failure due to “Leak 1 Trip” and shut itself down out of an abundance of caution. Upon further investigation the next day, Murry and I discovered there was a tiny split in one of the little hoses going into the GHU which was letting the electrolyte drip out.
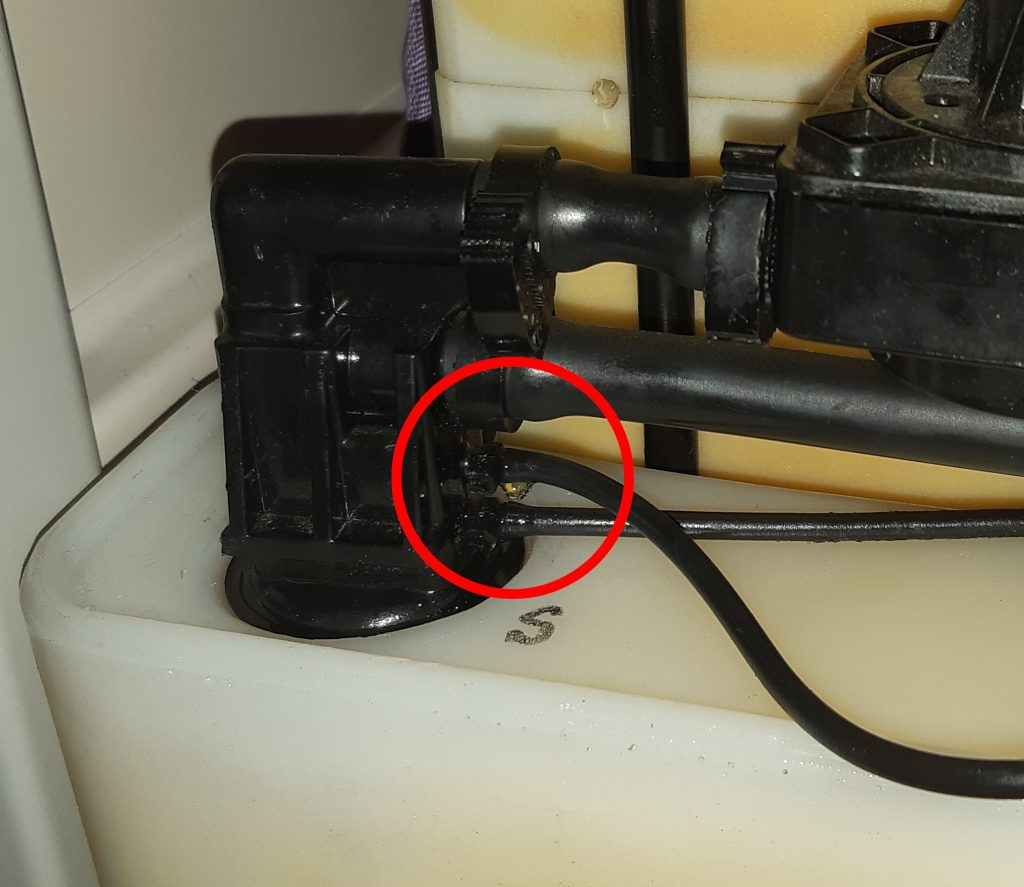
CC BY-SA Tim Serong

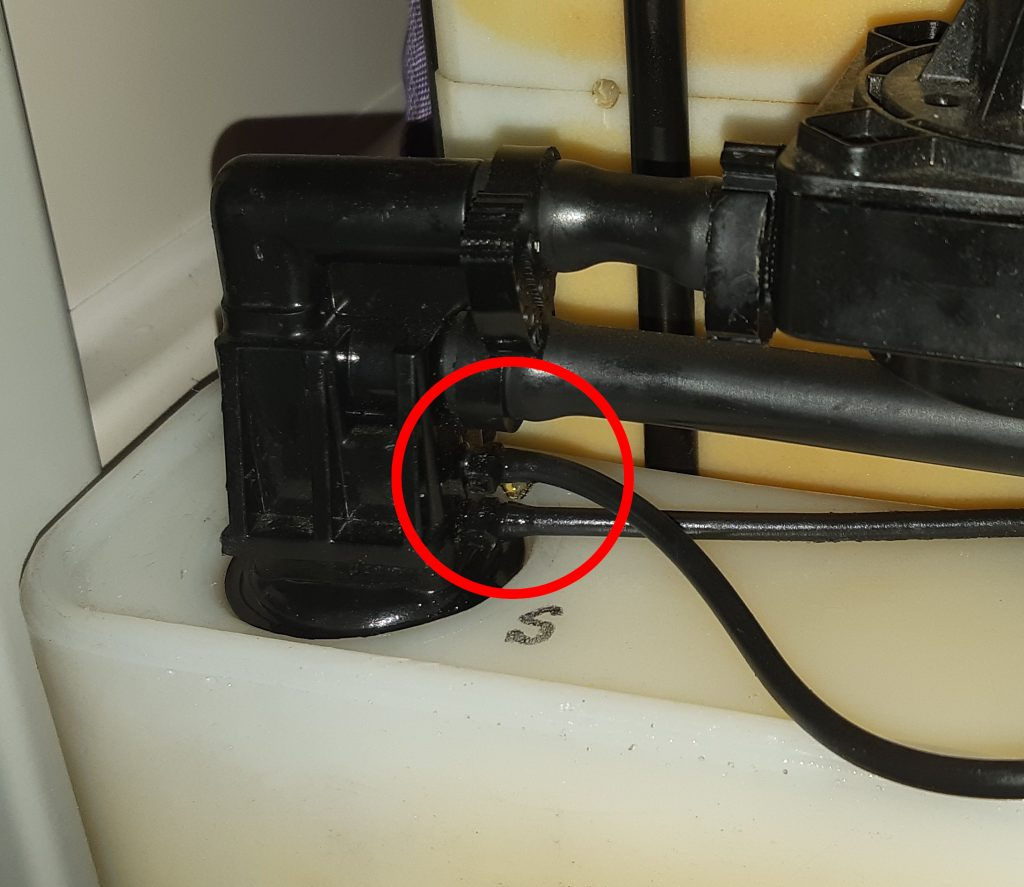
CC BY-SA Tim Serong
This small electrolyte leak was caught lower down in the battery, where the leak sensor is. Murray sucked the leaked electrolyte out of there, re-terminated that little hose and we were back in business. I was happy to learn that Redflow had obviously thought about the possibility of this type of failure and handled it. As I said to Murray at the time, we’d rather have a battery that leaks then turns itself off than a battery that catches fire! ... Aside from those two interesting events, the rest of the year of operation was largely quite boring, which is exactly what one wants from a power system.
Bearing all that in mind, my general advice to anyone else with a single ZCell system (aside from maybe adding scheduled charges to time-shift expensive peak electricity) is to just leave it alone and let it do its thing. You’ll use most of your locally generated electricity onsite, you’ll save some money on your power bills, and you’ll avoid some, but not all, grid outages. This is a pretty good position to be in.